
Mental changes in attitude towards the company as well as identification with goals and role expectations are to be triggered in all training phases.

The associated team dialogues based on case-related information boards (performance boards) are aimed at changing behaviour. While teaching modules that build on each other, such as problem-solving process, 5S and standards in a learning factory, can be easily presented in the technical qualification, performance management with its overall company understanding of causes and cost-related effects presents an overarching challenge. The pharmaceutical industry aims to follow the flow principle at the interface of production and logistics and to take into account learning contents of layout design and, in the future, the "pulling" control of batches with just-in-time (JIT) and just-in-sequence (JIS) mechanisms and inter-company supply chain management. This means that the third discipline, logistics, is called upon to convey the relevant requirements and methods in the learning factory. Ultimately, what counts for the customer is not only the required quality, but also delivery in the right quantity and on time. This task and the creation and continuous tracking of key performance indicators (KPI) in the production area falls within the specialist discipline of production management. The utilization of the plants depends on the technical availability and thus on the problem-solving ability of the maintenance staff and the line workers. Due to the high degree of automation in the process industry, the output and capacity utilization of the plants are cost-determining factors in addition to quality. One of the essential processes for ensuring quality is, for example, standardization, which can be assigned to the specialist discipline of quality management. In the pharmaceutical industry, for example, process reliability is the basis for customer confidence in the product and thus quality is non-negotiable. Therefore, the construction and operation of a learning factory requires several disciplines.
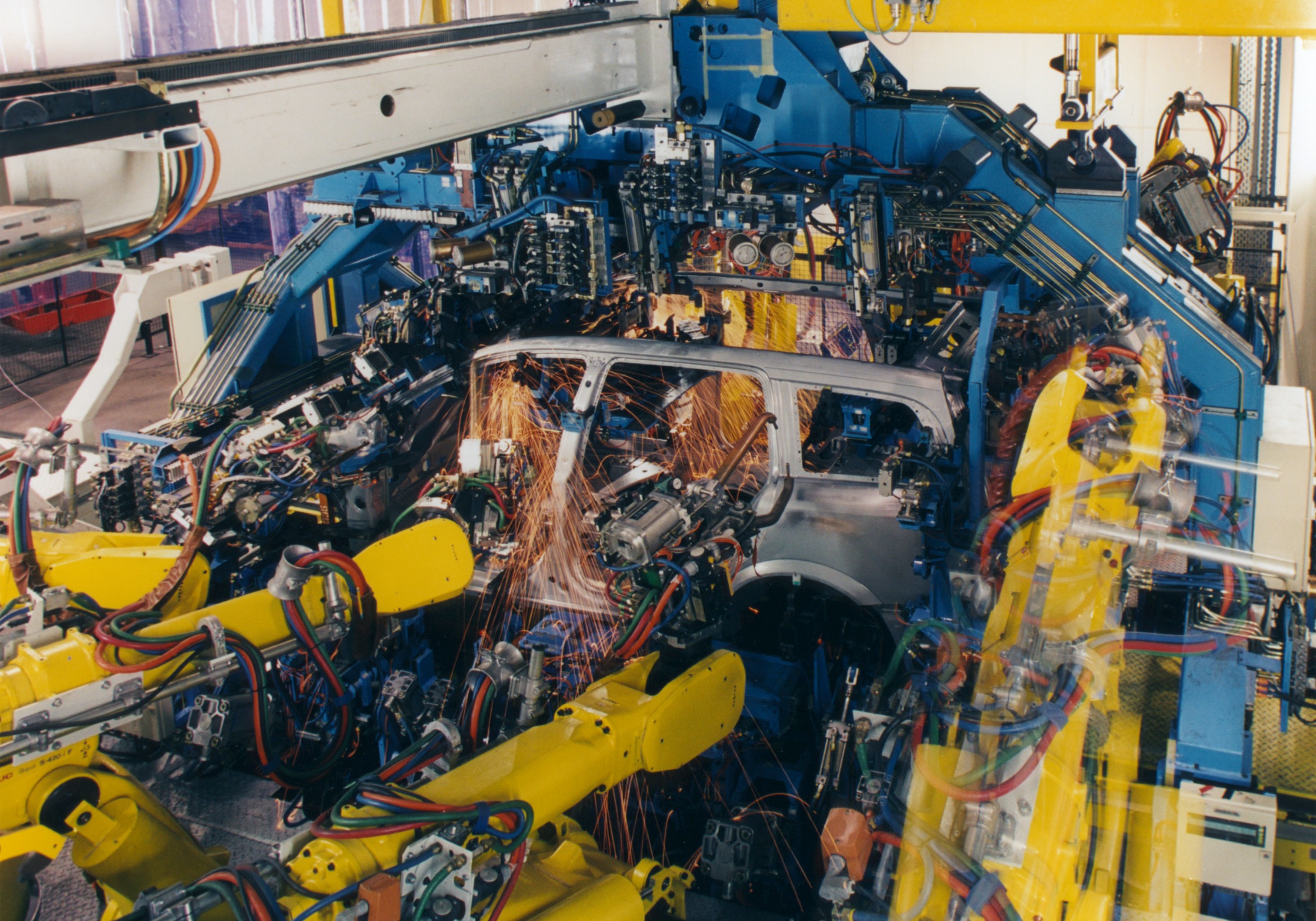
The specific methods and procedures of lean management cannot be assigned to just one specialist discipline. Within a learning factory, theoretically learned knowledge is applied within the framework of a realistic, participative and experience-oriented simulation and thus leads to the development of competencies. By setting up and operating a learning factory, this need for qualification can be secured in the long term. The design of such lean processes requires employees who are qualified to perceive problems in their own work environment as well as to continuously improve processes, but these are hardly available. The concept of "lean" aims at streamlining production processes by reducing waste.
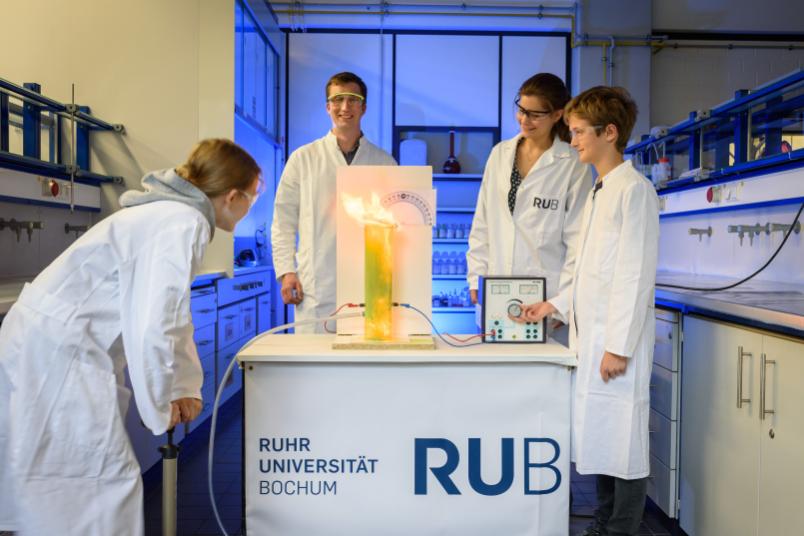
In this context, the concept of lean management has gained acceptance across industries. To counter these trends, pharmaceutical companies have begun to focus on internal structural changes, complexity reduction, and cost cutting. In turn, ever higher investments in research and development are necessary to keep the number of active ingredient approvals constant. For example, the expiration of patent rights for important drugs has led to declining sales and profits for pharmaceutical companies. The formerly stable environment of this has changed considerably in recent years. With almost 900 companies and 110,000 employees, the pharmaceutical industry is one of the oldest and most important sectors in Germany. Among the top 15 pharmaceutical companies in Europe in terms of turnover, German companies occupy a top position.
